Design Considerations for Optimizing Pogo Pin Female Connectors
Material Selection for High-Performance Pogo Pin Connectors
Key Materials in Pogo Pin Manufacturing
Material choice is pivotal in determining the conductivity and durability of pogo pins. As essential components in various electronic devices, pogo pins require materials that can sustain countless connect-disconnect cycles while ensuring a reliable electrical pathway. Copper alloys and stainless steel are frequently used for this purpose due to their excellent mechanical properties and resistance to corrosion. For instance, copper alloys offer superior conductivity which is crucial for efficient signal transmission, while stainless steel provides robustness against wear and environmental harshness. An industry report noted that using high-quality materials such as these can significantly extend the lifespan of pogo pin connectors, even in demanding applications.
Gold Plating vs. Nickel Alloys: Conductivity Comparison
When assessing conductivity, gold plating often outperforms nickel alloys, especially in high-frequency applications. Gold-plated pogo pins exhibit lower electrical resistance, making them ideal for environments where maintaining signal integrity is crucial. Statistical data suggest that gold-plated connectors have a longer lifespan, offering better performance in harsh conditions compared to nickel alloys. For example, gold-plated pins are frequently preferred in precision equipment due to their ability to remain reliable over many usage cycles. Market research points out that despite the higher initial cost, gold plating can prove more cost-effective in the long term due to reduced maintenance needs and prolonged connector life.
RoHS-Compliant Material Advancements
Compliance with the Restriction of Hazardous Substances (RoHS) directive is increasingly vital in pogo pin manufacturing. This legislation mandates a reduction in harmful substances such as lead, promoting the use of environmentally responsible materials. Recent advancements have led to the development of RoHS-compliant alternatives, allowing manufacturers to deliver eco-friendly options without compromising on performance. A report from industry regulators highlights the growing demand for green components as ecological concerns rise among consumers and industries. For manufacturers and end-users, these advancements not only ensure compliance with international regulations but also align with broader sustainability goals, reducing the environmental footprint of electronic components.
Mechanical Design and Durability Optimization
Spring Mechanism Engineering for 1M+ Cycles
To ensure pogo pins function reliably over a million cycles, spring mechanism engineering plays a pivotal role. By focusing on material properties and design, these mechanisms can withstand repetitive use without failure. The choice of durable materials and precise design helps in dampening material fatigue, a common challenge in high-cycle applications. For instance, some manufacturers have implemented proprietary designs that effectively reduce wear, achieving impressive longevity backed by test results. This engineering focus ensures the pogo pin connectors maintain optimal performance throughout their lifespan.
Tolerance Control (±0.01mm) Techniques
Achieving a precision of ±0.01mm in pogo pin production is crucial for the performance and reliability of the connectors. Tight tolerance control ensures that connections are firm and electrical paths are stable, preventing premature failures. Methods such as CNC machining cater to this demand by allowing precise cuts and consistency across production runs. Compliance with international standards for electronic components also underscores the importance of such precision, as even minor deviations can significantly impact the performance in sensitive applications like high-frequency signals.
Space-Saving Designs for Compact PCB Integration
The move toward space-saving design in pogo pins is driven by the demand for more compact and efficient PCBs, especially in portable tech devices. Innovative design approaches include reducing pin size and optimizing the arrangement without compromising functionality. As trends in consumer electronics lean into portability, such compact designs become essential. Successful implementations of these designs can be seen in devices like smartphones, where efficient space utilization contributes to the sleek and lightweight nature of modern gadgets. By focusing on miniaturization and efficiency, pogo pin connectors meet the industry's evolving needs.
Electrical Performance and Contact Reliability
Managing Contact Impedance Below 15mΩ
Managing contact impedance is crucial for the optimal performance of pogo pins in electronics. Achieving low contact impedance, ideally below 15mΩ, is essential as it enhances electrical performance by reducing power loss and ensuring efficient current flow. To attain this, manufacturers often employ gold plating on contacts, which minimizes resistance and improves connectivity. According to industry reports, devices with lower impedance demonstrate better performance and longevity. Testing methods, such as using low-resistance ohmmeters and specialized contact testers, ensure that pogo pins meet industry benchmarks for impedance.
High-Current Handling in Pogo Pin PCBs
Pogo pin connectors are designed to manage high current loads, a feature critical for many modern applications. These connectors can handle currents ranging from 2 to 8 amps, with specific designs supporting even higher ratings. High-current pogo pins are engineered to reduce thermal buildup, enhancing both the safety and reliability of electronic devices. Studies show that effective thermal management in high-current applications results in improved device durability. To ensure high-current reliability, manufacturers adhere to rigorous standards, including thermal cycling and current-carrying capacity tests. These protocols, largely adopted by top manufacturers, ensure that pogo pins maintain performance under increased electrical loads.
Preventing Signal Loss in High-Frequency Applications
Maintaining signal integrity in high-frequency applications poses significant challenges, particularly concerning signal loss. Design choices play a pivotal role in mitigating these issues; for instance, using materials with high conductivity and employing precise dimensional tolerances can reduce attenuation. Signal loss thresholds vary, but typically, less than 3 dB loss is desirable to maintain efficient data transmission. Companies focusing on minimizing signal loss often integrate advanced materials and geometrical optimizations into their pogo pin designs. Successful case studies show that with proper design configurations, pogo pins effectively mitigate signal degradation, ensuring reliable performance in high-frequency scenarios.
Featured Pogo Pin Connector Solutions
2 Pin Gold-Plated Connectors for Lead-Free Charging
The 2 Pin Gold-Plated Pogo Pin Connectors are specifically engineered for lead-free charging applications, offering enhanced reliability and conductivity. Gold plating is known for its excellent resistance to corrosion and superior conductivity, making these connectors highly reliable over long periods. The connectors' durability is exemplified in industrial applications where reliability is paramount, such as in medical electronics and digital cameras. According to performance data, using gold-plated connectors can reduce contact impedance, leading to more efficient power transfer and minimal energy loss. These attributes not only improve device performance but also extend the lifespan of the connectors in a variety of demanding environments.
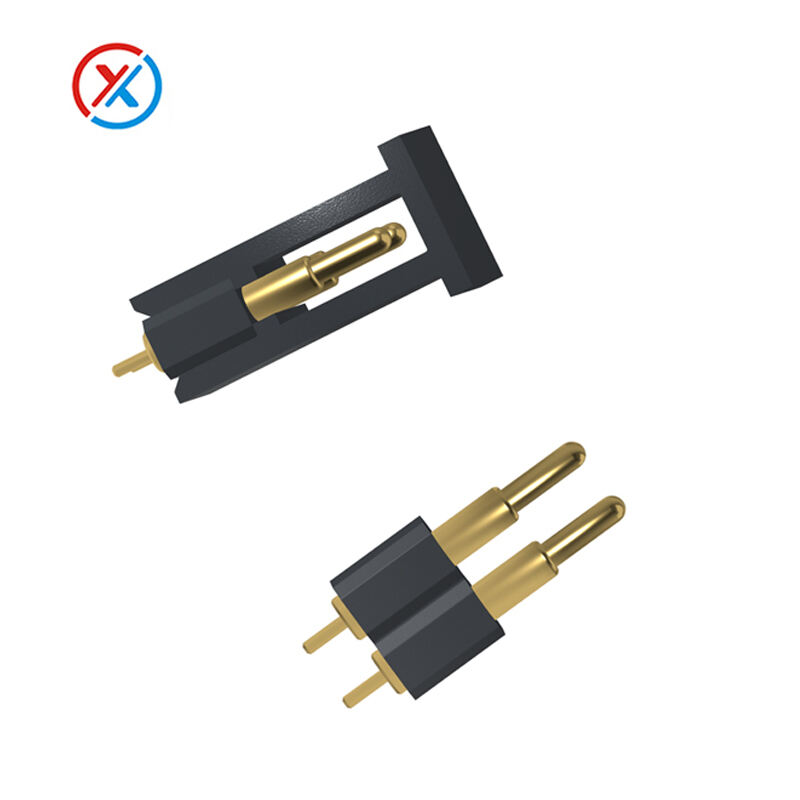
Male-Female Spring Connectors with Custom Elasticity
The male-female spring pogo pin connectors are designed with customizable elasticity, providing significant application versatility. Customization is achieved through precise engineering processes that allow adjustments in spring tension, meeting specific application needs. This flexibility benefits industries that require adaptable connections, such as consumer electronics and robotics. Positive user feedback has highlighted the connectors' effectiveness, such as reduced signal loss in high-frequency applications and enhanced durability under repeated use. The customizable nature of these connectors means they can be tailored to maintain optimal performance across various environments, leading to increased satisfaction and reduced maintenance issues.
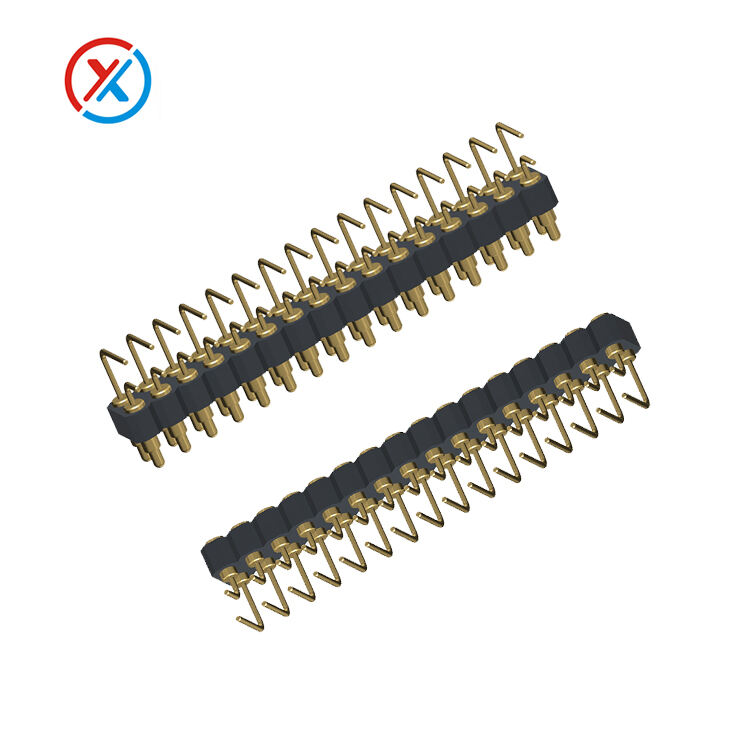
Addressing Complex Application Challenges
IP-Rated Designs for Harsh Environments
The significance of IP ratings in pogo pin connectors is paramount when determining their suitability for use in harsh environments. An IP (Ingress Protection) rating describes the degree of protection provided against dust, water, and other potential contaminants. For instance, connectors with an IP67 rating are designed to withstand dust ingress and immersion in water up to a specific depth, making them ideal for outdoor applications such as automotive and telecommunication settings. Notable examples include IP68-rated pogo pins used in marine electronics, where they ensure reliable performance even under prolonged submersion. These products often employ robust materials like stainless steel and incorporate sealed designs to withstand the challenges posed by demanding environments.
Customization Strategies for Unique Form Factors
Manufacturers adopt various strategies for customizing pogo pins to accommodate unique form factors, catering to diverse industry needs. Customization often involves tweaking dimensions, spring forces, and configurations to create connectors that seamlessly integrate with specific applications. For instance, tailored pogo pin designs can significantly enhance the efficiency of wearable technology, allowing for compact, lightweight assembly without compromising performance. Recent market trends indicate a growing demand for such bespoke solutions, driven by advancements in IoT and miniaturized electronic devices. Customer case studies frequently highlight the benefits of customization, such as improved device functionality and reduced manufacturing costs, underscoring its crucial role in today's gadget-intensive market.
Thermal Management in High-Power Scenarios
Thermal management poses notable challenges in high-power applications of pogo pin connectors, necessitating strategic design and material choices to ensure longevity. Heat generation can affect the connector's performance and lifespan, making effective thermal management vital. Manufacturers often utilize materials like copper alloys for their superior heat dissipation properties, alongside design features such as integrated heat sinks. For example, connectors used in data centers often include these techniques to handle the increased heat due to high-speed data transfer. Empirical data from industry studies shows that well-managed thermal solutions can extend connector life by up to 30%, demonstrating the importance of addressing heat concerns in high-power scenarios.
Hot News
-
Challenges for Pogo pin manufacturers in the AI era
2023-12-14
-
Teach you how to understand Pogo pin spline structure
2023-12-14
-
What products can Pogo pin be used in?
2023-12-14
-
How to choose Pogo pin connector
2023-12-14