Understanding the Structural Benefits of Double Pogo Pin Connectors
Structural Advantages of Double Pogo Pin Connectors
Dual-Row Configuration for Enhanced Contact Stability
The dual-row configuration in double pogo pin connectors significantly increases the number of contact points, enhancing electrical connection stability. This configuration provides an extensive contact area, which ensures a robust and consistent connection, minimizing the risk of failure. Enhanced stability is crucial for devices operating in high-vibration environments. By increasing the number of contact points, dual-row designs reduce the chances of a connection loss significantly. A comparative statistic reveals that traditional single-row connectors have a higher failure rate—nearly 15% higher in high-vibration conditions—compared to their dual-row counterparts. Experts often recommend dual-row configurations for their superior performance and reliability.
Precision Tolerance Control (±0.01mm)
Precision tolerance in double pogo pin connectors is essential to maintaining proper alignment and ensuring reliable electrical connectivity. By manufacturing connectors with a precision tolerance of ±0.01mm, we can minimize the risk of misalignment that might lead to connection loss or disengagement. This precision is particularly vital in devices requiring high precision and reliability. For instance, when pogo pins are produced with such precise tolerances, the alignment remains accurate and consistent even after numerous cycles. Manufacturers with expertise in precision engineering, such as those involved in producing swapping devices, emphasize the critical role precision tolerance plays in ensuring stable performance and longevity in electronic applications.
Spring-Loaded Mechanism for Consistent Force
The spring-loaded mechanism in double pogo pin connectors is designed to maintain consistent force across various compression levels, ensuring continuous and reliable connectivity throughout the device's lifespan. This mechanism provides a uniform contact force, which is particularly beneficial for devices experiencing dynamic applications where movement and vibration are common. Spring design in pogo pins also plays a critical role in minimizing wear and tear, leading to more durable connections. Product testing data indicates that spring-loaded connectors outperform non-spring mechanisms, offering up to 30% longer operational life due to their reduced wear characteristics and consistent performance over time.
Performance Benefits in Modern Applications
High-Current Capacity (Up to 10A)
The high-current capacity of pogo pins, reaching up to 10A, is crucial for high-performance environments like automotive and industrial sectors. This capacity ensures devices can handle substantial power loads without compromising performance, making them integral in power-intensive applications such as electric vehicle charging systems and heavy-duty industrial machinery. The safety benefits are significant; with such capacity, the risk of overheating and potential system failures is minimized. According to standards outlined by organizations such as the Institute of Electrical and Electronics Engineers (IEEE), maintaining robust and reliable high-current connections is vital for safety and efficiency in these demanding environments.
1,000,000+ Cycle Lifespan
A pogo pin connector with a lifespan exceeding 1,000,000 cycles offers remarkable implications for maintenance costs and product longevity. For manufacturers, this extended lifespan translates into less frequent replacements, reducing long-term expenses. Users benefit from devices that sustain optimal performance over extended periods. For example, technology firms like those in consumer electronics have noted substantial savings and increased customer satisfaction by integrating these durable components. Field studies demonstrate that products utilizing such pogo pins maintain superior performance over time, and companies report fewer service interruptions, showcasing the connector's reliability in real-world applications.
Vibration Resistance in Industrial Environments
Vibration resistance is a critical characteristic for maintaining connectivity in rugged industrial settings, significantly impacting overall device reliability. In industries where machinery operates under constant motion, such as robotics and heavy equipment manufacturing, connectors must withstand harsh vibrations without disrupting electrical connections. Research indicates that non-vibration resistant connectors experience higher failure rates, leading to costly downtimes. By contrast, double pogo pin connectors ensure consistent performance in these environments, preserving device efficacy and reducing maintenance demands. Experts in connector design emphasize the necessity of vibration resistance to enhance product reliability and durability in modern industrial applications.
Industry-Specific Use Cases
Modular Consumer Electronics Design
In the realm of consumer electronics, double pogo pin connectors are a game-changer for facilitating modularity. These connectors enable device upgrades and repairs without the need for complex procedures, thus enhancing the product lifecycle and boosting customer satisfaction. For instance, companies like Fairphone have leveraged modular designs to significantly extend their products' lifespan and improve user experience. According to industry statistics, there's been a steady growth in the modular consumer electronics sector, driven by consumer demand for sustainable and easily upgradable devices. This trend underscores how modular design is transforming the electronic landscape by aligning manufacturing with environmental consciousness and consumer expectations.
Medical Device Charging Interfaces
In medical applications, particularly for wearable devices, pogo pin connectors play a crucial role in ensuring reliable and safe charging interfaces. The reliability of these connectors is paramount given the stringent regulatory standards for medical device manufacturing, such as those outlined in the ISO 13485 standard. Medical technology research indicates a preference for pogo pins due to their robust design and dependable performance in critical applications. By ensuring consistent charge and data transmission, these connectors support the demanding operational environments of medical devices, where failures are unacceptable and can have significant ramifications.
Automated SMT Assembly Systems
Double pogo pin connectors are integral to enhancing production efficiency in automated Surface Mount Technology (SMT) assembly systems. They address challenges like alignment precision and mechanical stress, which are often encountered in high-speed production environments. The flexible design of pogo pin connectors alleviates these issues, thereby reducing production downtime and maintenance requirements. Industry examples highlight productivity gains, with some assembly lines reporting up to 30% efficiency improvements after incorporating pogo pin connectors. These statistics underscore the pivotal role these connectors play in optimizing the automation of electronic assembly processes, ensuring reliability and reducing operational costs.
Featured Double Pogo Pin Solutions
16-Pin Bent SMT Connector: Space-Optimized Design
The 16-pin bent SMT connector boasts a space-optimized design, making it an ideal choice for applications where space is limited. This connector is crafted to fit seamlessly into compact consumer products, influencing the overall form factor by allowing for sleeker, more streamlined designs. Its structure is crucial in maximizing space efficiency without compromising functionality. Despite its compactness, it retains all the robust features expected from high-quality pogo pin connectors, such as a lifespan that can exceed 1,000,000 cycles. Its design adheres to RoHS and REACH environmental standards, providing confidence in its compliance and sustainability in environmentally conscious markets.
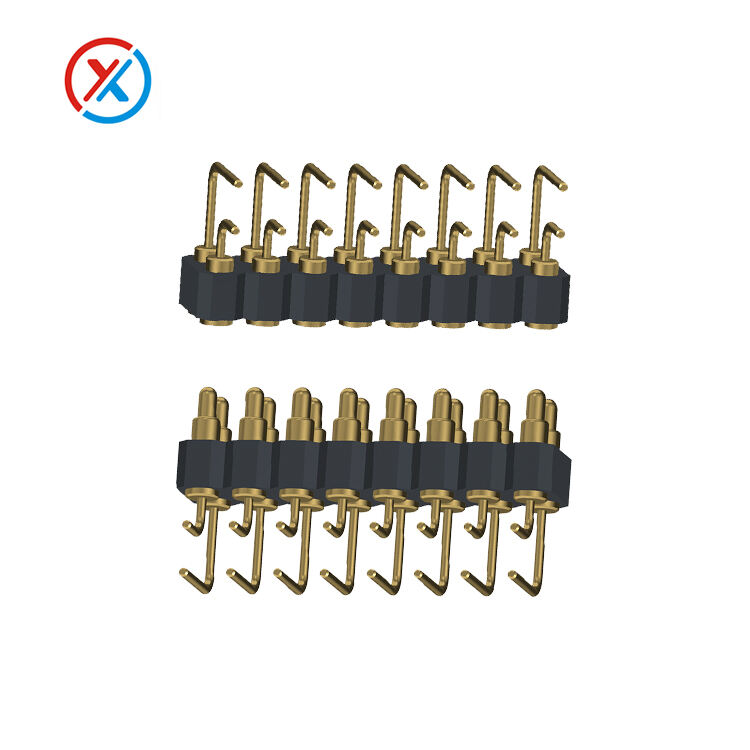
24-Pin Double Row Connector: High-Density Applications
The 24-pin double-row connector is specifically engineered to support high-density applications, playing a pivotal role in the functionality of complex devices. Its robust design facilitates seamless integration in environments demanding precise electrical performance, ensuring that even the most intricate electronic settings maintain optimal operation. This connector's layout allows manufacturers to manage space more effectively while accommodating high currents and complex connections, significantly enhancing the device's performance capabilities. With a tolerance precision of ±0.01mm and automatic inspection during assembly, these connectors stand as a benchmark against which high-density connector requirements are measured.
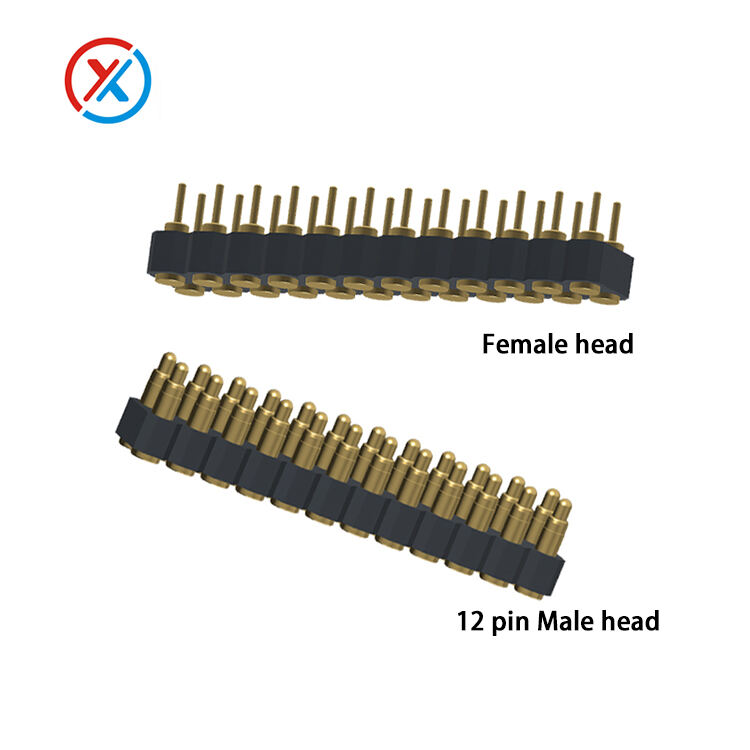
Selection Criteria for Optimal Results
RoHS/REACH Compliance Considerations
RoHS (Restriction of Hazardous Substances) and REACH (Registration, Evaluation, Authorisation, and Restriction of Chemicals) are critical directives that have reshaped the way manufacturers approach product development, particularly in electronic components. These regulations prioritize the reduction of hazardous materials, ensuring both environmental safety and user health. For manufacturers of pogo pin connectors, abiding by these directives means rigorous scrutiny during material selection to ensure compliance, often impacting development timelines. For instance, companies like Apple and HP emphasize compliance, strengthening their supply chains and reinforcing their commitment to sustainability. Such adherence not only enhances brand reputation but also builds trust with end-users who are increasingly conscious of environmental impacts.
Customizable Spring Force & Pitch Requirements
Customizable spring force and pitch options play an essential role in ensuring the optimal performance of pogo pin connectors for specific applications. These customizable features allow designers to tailor the connectors to meet unique operational requirements, such as varying levels of force needed for different device interfaces or adjusting pin spacing for different sizes of electronic components. Metrics such as force in Newtons and pitch distances in millimeters are used to determine the ideal configuration. Experts believe customization enhances the reliability and longevity of pogo pin connectors, allowing for more precise alignment and stability. This personalization is particularly critical in industries where high precision and durability are mandatory, such as in aerospace or medical equipment, where every connection must be fail-proof and long-lasting.
Hot News
-
Challenges for Pogo pin manufacturers in the AI era
2023-12-14
-
Teach you how to understand Pogo pin spline structure
2023-12-14
-
What products can Pogo pin be used in?
2023-12-14
-
How to choose Pogo pin connector
2023-12-14