Exploring the Mechanical Strength of Large Pogo Pins
Factors Influencing Mechanical Strength in Large Pogo Pins
Material Composition and Durability
The mechanical strength of pogo pins is significantly enhanced by carefully selecting materials such as copper, nickel, and gold. Copper is often favored due to its excellent electrical conductivity and durability under stress, while nickel offers additional corrosion resistance. Gold is typically used for plating as it prevents oxidation and reduces contact resistance, ensuring long-term reliability. Studies have shown that alloy choices can profoundly impact the durability of pogo pins, especially in high-stress environments. Moreover, fatigue resistance plays a crucial role in determining the longevity of pogo pin connectors, as the material must withstand numerous compression cycles without degrading.
Spring Force and Elasticity Adjustments
The variation in spring force is fundamental to the mechanical performance of pogo pins. Precise control of spring force ensures that the contact points maintain their integrity through numerous connection cycles, preventing loosening or loss of connectivity. Elasticity adjustments are equally important as they help maintain optimal contact pressure during repetitive use, thereby enhancing durability. In industrial applications, there is an established range for optimal spring force, which ensures pogo pins can handle mechanical stress while maintaining a reliable connection. These adjustments are critical in crafting robust pogo pin connectors that meet the stringent demands of various applications.
Impact of Plating on Corrosion Resistance
Plating techniques, such as using gold or nickel, significantly affect the corrosion resistance of pogo pins, thereby extending their lifespan. Gold plating, in particular, provides a superior barrier against oxidization and environmental wear, maintaining electrical performance over time. Statistical analyses suggest a substantial increase in product life when proper plating techniques are employed. Industry standards demand these robust plating processes, especially in high-stress environments where pogo pins must withstand constant friction and contact with various materials. Such standards ensure that these connectors offer long-lasting, reliable performance across different applications.
Testing Methods for Pogo Pin Mechanical Integrity
Cycle Life Testing (1,000,000+ Compressions)
Cycle life testing is a crucial method to assess the durability and mechanical integrity of pogo pin connectors. This testing involves subjecting the pogo pins to over a million compressions to simulate extensive use and ensure their reliability over numerous cycles. Such rigorous testing provides invaluable data demonstrating the longevity and consistent performance expected from high-quality pogo pins connectors. Various methodologies are employed to perform cycle life tests accurately, including automated machines that consistently apply and release pressure to reflect real-world usage scenarios, allowing manufacturers to refine their designs for optimal durability.
Environmental Stress Simulations (Salt Spray, Temperature)
Environmental stress testing, including exposure to salt spray and extreme temperatures, is vital for evaluating the resilience of pogo pins to real-world conditions. These simulations replicate harsh environments to test the endurance of pogo pins and are instrumental in understanding how these pins perform under duress. Research findings have consistently shown that such environmental tests offer insights into potential failure rates, aiding in the design of more robust products capable of withstanding challenging conditions. The correlation between testing conditions and product failure rates underscores the importance of these simulations in developing pogo pins that can maintain their integrity across various applications.
Applications Demanding High-Strength Pogo Pin Connectors
Smart Devices: Charging and Data Transfer
In the realm of smart devices, high-strength pogo pin connectors play a crucial role in ensuring efficient charging and reliable data transfer. These connectors, often utilized in magnetic connector assemblies, provide seamless and secure connections that enable rapid charging and transfer of data without the wear and tear typically associated with repeated plugging and unplugging. For instance, magnetic USB chargers in smartphones exemplify the utilization of pogo pin connectors, where their consistent contact pressure ensures a stable connection. Moreover, these pins are designed to maintain their integrity over thousands of cycles, making them ideal for maintaining connections in various smart technologies.
Industrial Automation and Ruggedized Equipment
High-strength pogo pins significantly enhance the performance and reliability of industrial automation systems and ruggedized equipment. In industrial settings, these connectors are used to withstand harsh environmental conditions while ensuring continuous operation. Ruggedized equipment, such as automated machinery in manufacturing plants, often incorporates pogo pin connectors for their ability to maintain reliable connections in dusty, moist, or high-vibration environments. The industry demands connectors that can endure such conditions without degradation, and pogo pins meet these requirements due to their durability and robust design. Whether in factory automation or outdoor telecom installations, the use of pogo pins helps ensure consistent operations and minimize downtime.
Large Pogo Pins Surface Mount 12V DC-1204: A Case Study
Key Features: 80g×20g Elastic Force, 100V Rating
The 12V DC-1204 pogo pins are renowned for their critical attributes that cater to versatile applications, notably featuring an elastic force of 80g ± 20g. This component is imperative as it not only facilitates a secure connection but also ensures that disconnections are smooth and safe. The voltage rating of 100V further enhances its reliability and safety, making these pogo pins suitable for varying power demands while minimizing potential risks, thereby improving performance. User testimonials highlight the effectiveness of these pins in applications such as smartphones and smartwatches, where durability and consistent conductivity are vital for enhancing device functionality. The Large Pogo Pins Surface Mount 12V DC-1204 demonstrates the advanced capabilities and adaptability, proving to be a reliable choice for many technological needs.
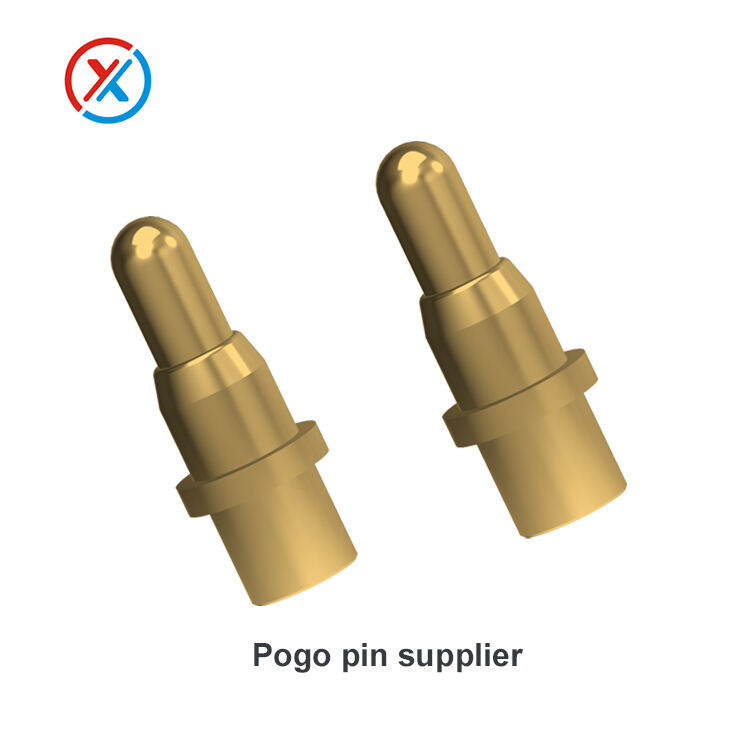
Customization Options for Magnetic Connector Integration
Customization is a significant advantage in the realm of pogo pins, particularly when integrating magnetic connectors. This flexibility allows the 12V DC-1204 model to be tailored for diverse applications, enhancing compatibility across various devices and systems. By customizing features such as shape structure and material properties, manufacturers can achieve specific conductivity, elasticity, and mechanical requirements crucial for optimal performance. Examples abound in tech industries, such as smartphones and wireless headphones, where customized pogo pins enable efficient magnetic connector integration without compromising space or connectivity reliability. Through this capability, these pins facilitate innovative solutions in precise and demanding environments.
Performance in High-Density PCB Applications
In high-density PCB (Printed Circuit Board) applications, the performance of pogo pins like the 12V DC-1204 cannot be overstated. Their design facilitates superior space management, enabling integration into tightly packed boards without sacrificing efficiency. The spring-loaded mechanism ensures minimal force requirement, thereby reducing stress on components while maintaining high contact reliability. Data from benchmarks indicate that these pogo pins offer reduced impedance and enhanced durability, contributing to robust performance in complex electronic setups. This unique feature aligns with industry needs for compact and efficient circuit solutions, making them indispensable in cutting-edge electronic configurations.
Advantages of Precision-Engineered Pogo Pin Solutions
Space-Saving Designs with ±0.01mm Tolerance
Precision-engineered pogo pins offer significant space-saving advantages for compact and intricate designs. By maintaining a tight tolerance of ±0.01mm, these connectors can be effortlessly integrated into complex systems without compromising on performance. Industries like aerospace and medical devices, where space is a premium, heavily rely on such precise components for optimal functionality. Studies in industrial engineering underscore how even slight variations in tolerance can impact the overall efficiency and reliability of a system. Thus, utilizing precision-engineered pogo pins ensures that systems are not only spatially efficient but also robust and dependable.
Enhanced Signal Integrity Through Low Contact Resistance
Low contact resistance is crucial for maintaining robust signal integrity in pogo pin connectors, directly impacting their overall performance. These connectors promise enhanced signal quality by minimizing resistance at the contact points, crucial in an era where reliable connectivity is paramount. According to studies, reducing contact resistance leads to a noticeable improvement in signal clarity and data transmission efficiency. As the demand for steadfast connectivity grows, especially in industries relying on accurate data transfer, the advantage of low-contact-resistance pogo pin solutions becomes irreplaceable. This advancement ensures that systems operate smoothly, accommodating the increasing complexities of modern digital infrastructure.
Hot News
-
Challenges for Pogo pin manufacturers in the AI era
2023-12-14
-
Teach you how to understand Pogo pin spline structure
2023-12-14
-
What products can Pogo pin be used in?
2023-12-14
-
How to choose Pogo pin connector
2023-12-14